March 17th, 2020
7 best practices small to mid-sized manufacturers are implementing to mitigate the effects of COVID-19
As our region’s economy begins to grapple with the effects and uncertainty presented by COVID-19, many small to mid-sized manufacturers are sharing the best practices they have begun to implement to deal with this unprecedented situation. The following is a list of options and steps your business can consider as we work collaboratively to mitigate the negative impact of COVID-19.
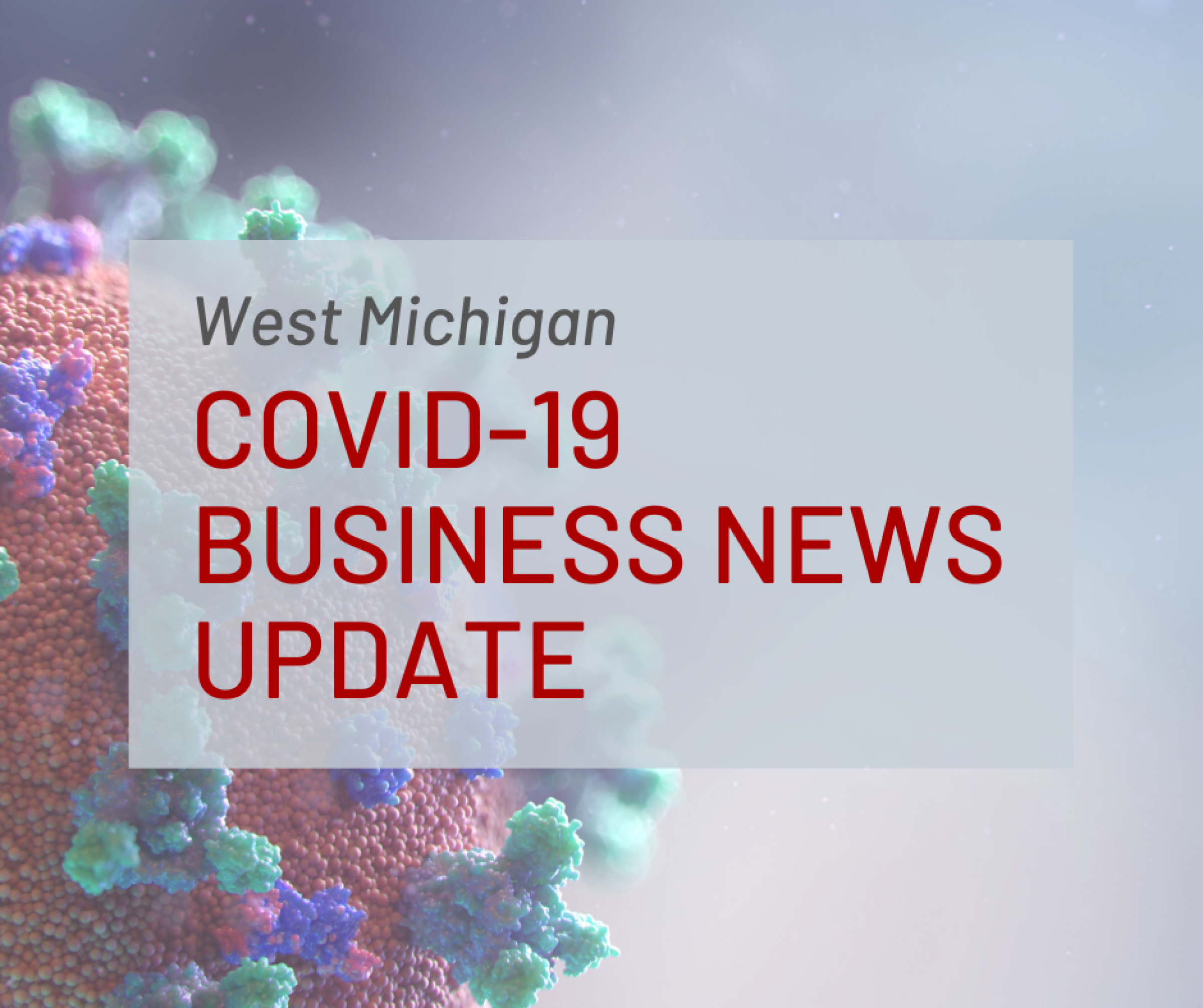
As our region’s economy begins to grapple with the effects and uncertainty presented by COVID-19, many small to mid-sized manufacturers are sharing the best practices they have begun to implement to deal with this unprecedented situation. The following is a list of options and steps your business can consider as we work collaboratively to mitigate the negative impact of COVID-19. Each business is unique and not all options may fit your needs, but it is a starting point.
As always, the team at The Right Place is available to assist you with specific questions and connect you to the resources needed to weather this storm. Please reach out to individual team members or contact us via our contact form. Our services are completely confidential.
- Implement Emergency Response Plans – If your company has an emergency response plan designed to deal with a pandemic, now is the time to begin implementing the action steps. Alternatively, if you do not have a response plan, it is not too late to craft one and begin implementation.
- Maximize Remote Work Options – Many factories and offices have moved to remote work whenever possible. Companies are also utilizing a rotating cohort of key staff to maintain critical business functions at facilities. In operations where remote work is not possible, social distancing measures are being implemented.
- Limit/Ban Travel and In-person Meetings – Companies are utilizing teleconferencing in place of in person meetings, with resources such a GoToMeeting, Microsoft Teams, and Google Hangout. They are also restricting vendor and visitor meetings to their facilities. Travel is being curbed to only critical needs.
- Temperature Monitoring – In facilities where employees must be present physically, employers have begun mandatory fever testing and sending anyone home who presents with a fever.
- Revise Sick Leave Policies to Reflect Coronavirus- Manufacturers are revising sick policies to deal with the realities of unexpected sickness and childcare needs, particularly due to mass school and daycare closings. Manufacturers are considering shift changes such as adding weekend and 3rd shifts to allow operations to continue running smoothly. Consider utilizing temporary help services.
- Sanitization Measures – Manufacturers are implementing aggressive sanitization measures to protect the health and safety of their workers throughout the facility.
- Stay Informed of Available Resources: There are many resources available to assist your business and workers during this time, and new assistance is becoming available. Currently, The Small Business Administration has included Coronavirus as a qualifying disaster for receiving Economic Injury Disaster Loans. Manufacturers needing liquidity may want to utilize this option. Additionally, unemployment benefits have been expanded by the Governor of Michigan to cover Coronavirus-related issues.