December 4th, 2024
Eagle Alloy: Training Boosts Efficiency & Productivity
Through MMTC partnerships, Eagle Alloy created a tailored upskilling program for their workforce, addressing the skills gap and improving overall efficiency and productivity
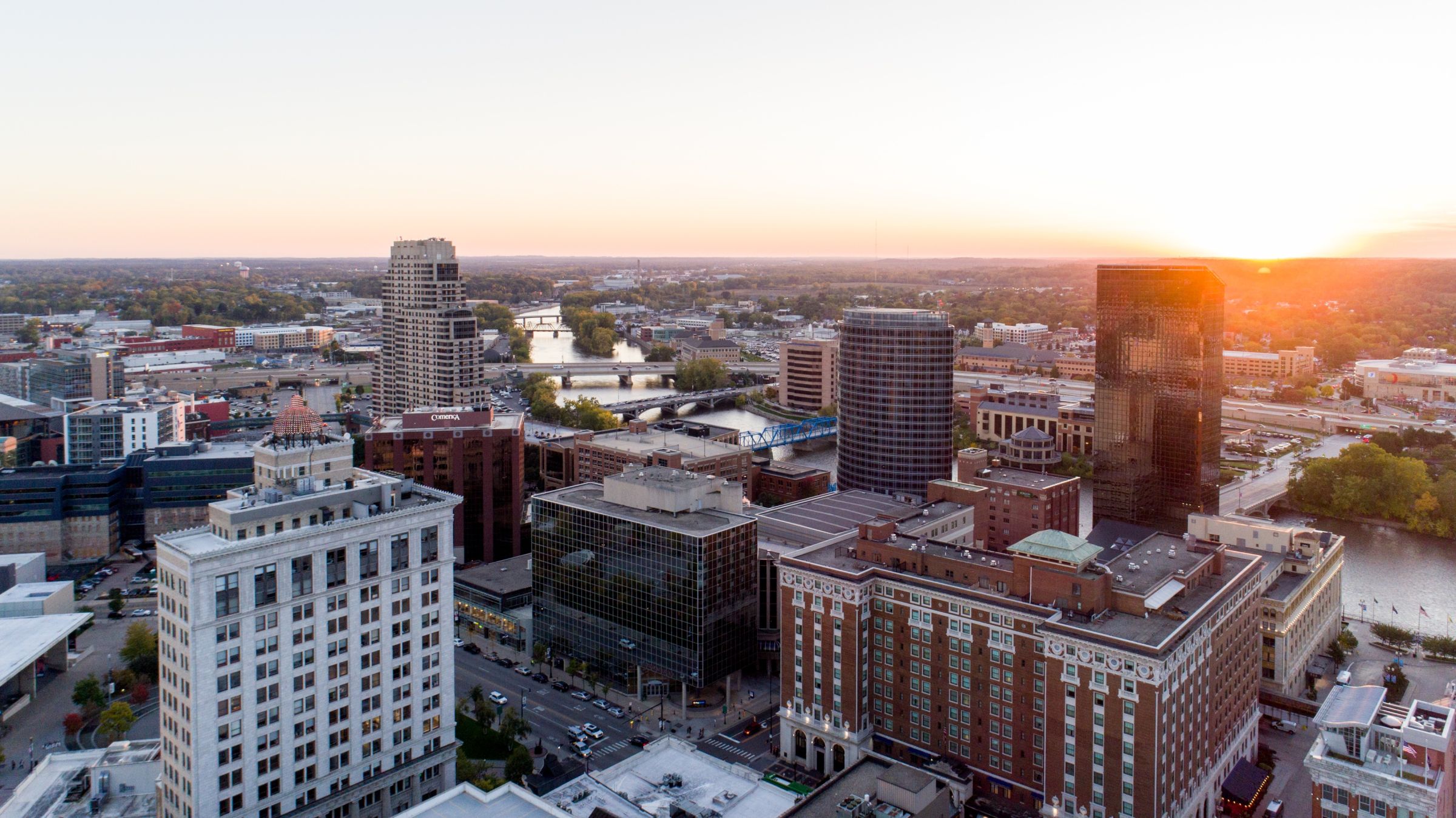
Based in Muskegon, Mich., Eagle Alloy, Inc. (www.eaglealloy.com) is a leading steel casting manufacturer with approximately 250 employees. Founded in 1979, Eagle Alloy operates as part of Eagle Group, which includes sister companies specializing in different aspects of metal manufacturing. The company serves various markets, including agricultural, construction, and energy industries, providing high-quality steel castings and machined components to clients across the U.S. and internationally.
Situation
Over a three-year period, Eagle Alloy faced a significant challenge when several long-term employees from their engineering department retired. This turnover created an urgent need to rebuild the department and bridge a critical skills gap left by departing team members. Recognizing the potential impact on their operations and competitive edge, Eagle Alloy’s leadership sought assistance to develop a strategic approach to recruit, train, and equip new engineering talent, ensuring the continuity of their high standards in steel casting production and innovation.
Solution
Through Michigan Manufacturing Technology Center (MMTC) partnerships, Eagle Alloy created a tailored upskilling program for their workforce. Several internal employees enrolled in courses focused on robotics and PLC (Programmable Logic Controller) training, equipping them with critical technical skills that were previously held by the retired engineering team. This targeted training not only addressed the immediate skills gap but also improved overall efficiency, increased productivity, and enhanced the company’s agility.
With these newly trained team members, Eagle Alloy is now better prepared to navigate future employment shifts and uphold high standards in their production processes. Additionally, with enhanced technical capabilities, Eagle Alloy expanded its market opportunities, generated new sales, and retained critical jobs within the company, reinforcing their adaptability to ongoing workforce changes.
Results
Retained Sales: $500,000
New Investment: $100,000
Jobs Retained: 4
Cost Savings: $115,000
New Sales: $30,000
Jobs Created: 1
Client Testimonial
“I am grateful for the support we received from MMTC. Their dedication and expertise had a significant impact on addressing our organization’s training needs, equipped our team with vital skills, and instilled confidence in our employees. Thanks to MMTC, we are now better positioned to meet our technical demands and continue growing as a company. I wholeheartedly recommend their services to any organization seeking to enhance their training programs.” - Nic Tarzwell, Chief Technical Officer