August 20th, 2019
Manufacture Smarter: Is training really the key to making gains in manufacturing?
As with any business environment, continued learning should be an integral part of the overall business plan. Training should be an equal part of the improvement and investment plan that a company creates and revises each year.
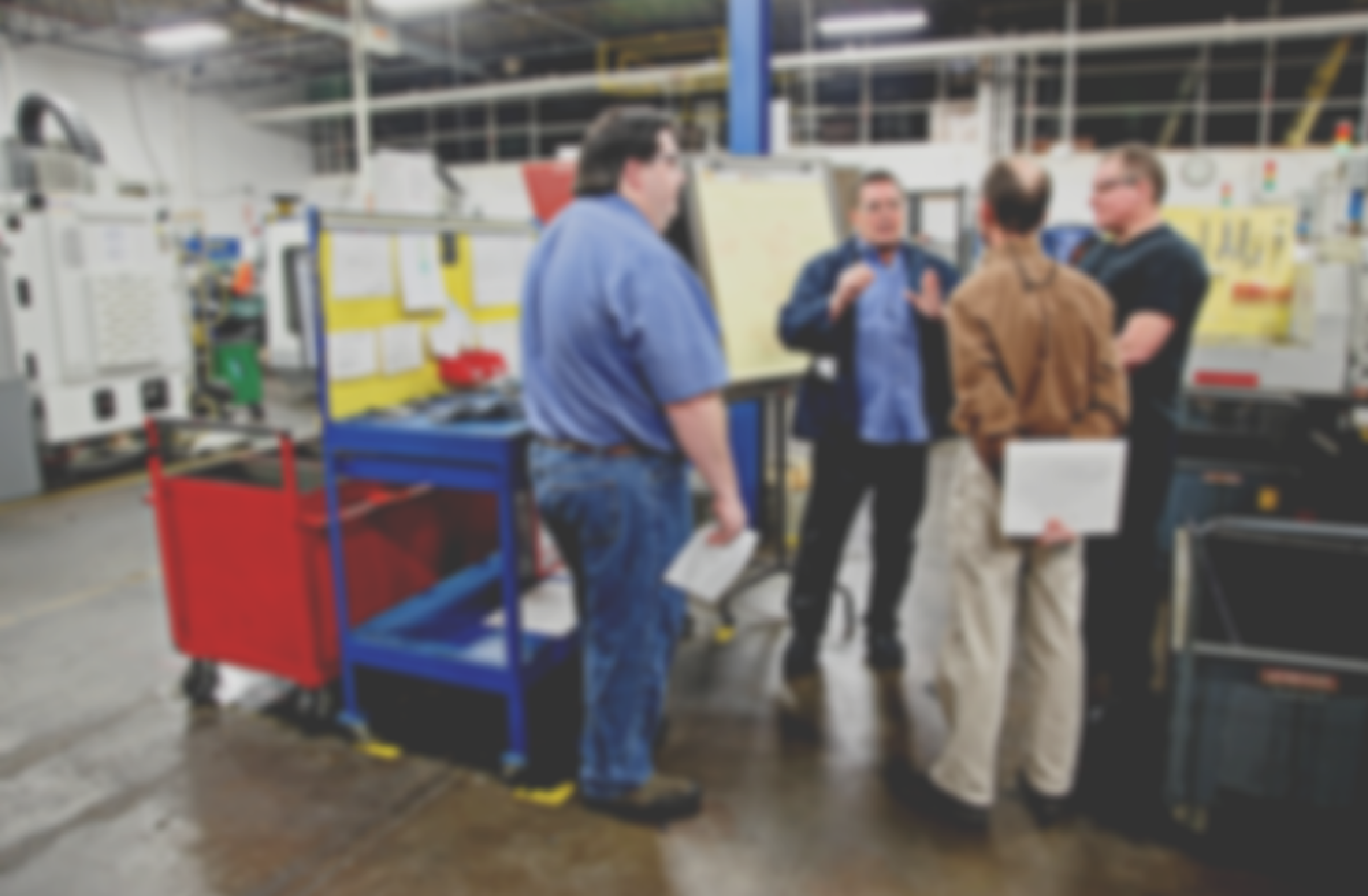
Is training really the key to making gains in manufacturing?
I work for The Michigan Manufacturing Technology Center (The Center), a consulting and training organization, so you probably assume that I’ll say yes. The truth of the matter, however, is that the answer is really something along the lines of, “Yes, but…” As with any business environment, continued learning should be an integral part of the overall business plan. Training should be an equal part of the improvement and investment plan that a company creates and revises each year.
Proven Success
I have 30+ years of manufacturing leadership experience, both with small, family-owned operations and a Fortune 50 company. During that time, I found each company to have a different approach towards investment strategy, especially as it pertains to continued learning. The efficacy of their approaches had little to do with company size, as there were similar beliefs and learning investment strategies across the board.
Part of what made the companies I’ve worked for successful was a vision of investing in their workforce. Education was a significant part of their budgets, which benefitted continuous improvement in cost, safety performance, retention rates and customer satisfaction. Alternatively, I’ve also seen the opposite happen, when new owners made the decisions to drastically reduce investments in continued learning. In a few short years, most of the gains previously achieved were reduced or disappeared entirely. As a result, continual cost improvement stagnated, and margins reduced.
As the manufacturing world becomes increasingly competitive and a short supply of labor affects businesses around the globe, investment in human capital has become imperative. The gains that can be made from upskilling your employees tend to outweigh the cost of seeking and hiring new talent. With your current workforce already knowledgeable about the company, its products and processes, you save yourself the cost of having to reteach those things to someone new.
The Future of Work
Good investment strategy should include an upskilling plan for employees at every level of the organization. The manufacturing and business worlds of today are part of a rapidly changing environment, so your workforce, from top to bottom, has to be prepared to adapt.
Industry 4.0 is significantly altering the future of manufacturing. As technologies and demand shift in this era of automation, the more knowledgeable and adaptable your workforce is, the easier it will be for your company to remain competitive. Pragmatically speaking, the chances of having already-prepared external talent at your disposal are low.
Talent investment assistance is an excellent resource offered by the State of Michigan via Michigan Works! offices and the Going PRO Talent Fund. Companies looking for resources to fund talent improvement and transition are able to take advantage of these offerings.
Author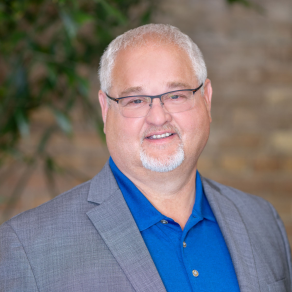
Terry Hossink
Vice President, Manufacturing ServicesTerry is responsible for The Right Place’s Manufacturing Services team. He is also the Regional Director for the Michigan Manufacturing Technology Center - Grand Rapids office team. This team works with West Michigan’s small and mid-sized manufacturers assisting them with their opportunities for continuous improvement, development, growth, and transition with advanced manufacturing technologies.
Full Bio
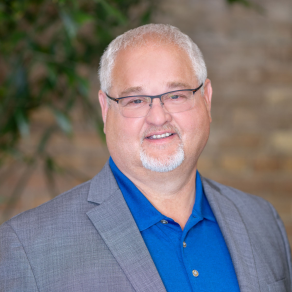
Terry Hossink
Vice President, Manufacturing ServicesTerry is responsible for The Right Place’s Manufacturing Services team. He is also the Regional Director for the Michigan Manufacturing Technology Center - Grand Rapids office team. This team works with West Michigan’s small and mid-sized manufacturers assisting them with their opportunities for continuous improvement, development, growth, and transition with advanced manufacturing technologies.